We will be sharing with you tips by which, a hose maintenance process will become easy. Along with that, we will also share the importance of hose maintenance.
You may have carefully selected the hose and assembled it, but without a proper maintenance, it might not last as long as it should. What you need is a continuous hose maintenance program to reduce the risk of sudden failure and damages.
Importance of Continuous Hose Maintenance
Hose maintenance is the inspection of hose and hose assembly to ensure safety, productivity and long service life. It should be a continuous cycle. A continuous hose maintenance can help achieve the following benefits,
- Reduces equipment downtime
- Maintains peak operating performance
- Reduces risk of personnel injury
- Prevents property / equipment damage
The user should design and implement a maintenance program that suits the specific application and each specific hose in that application.
Doing a continuous hose maintenance you can prevent these above damages and ensure effective operations. Knowing in advance about a failure can help you prepare for it and mitigate loss of time and resources.
Inspection Frequency
Continuous needs a time frame and it is not easy to decide the frequency of a hose maintenance program.
Running a hose maintenance program, also means either slowing or shutting down the operation. This has its own consequences. These factors and help you evaluate the situation and decide the frequency of the program.
- Nature of Application
- Severity
- Past History and Causes of Breakdowns and Failures
- Manufacturer’s Guidelines
You can conduct the inspection in two methods,
- Visual Inspection
- Functional Tests
Visual Inspection
It refers to visually inspecting the hose assembly for the following signs
- Leaks in hose fittings or the hose itself
- Damaged, cut or abraded cover
- Exposed reinforcements
- Kinked, crushed flattened or twisted hose
- Hard, stiff, heat cracked or charred hose
- Blistered, soft, degraded or loose cover
- Cracked, damaged or badly corroded fittings
- Fitting slippage on hose
- Excessive dirt and debris around hose
- System fluid: level, type, contamination, condition and air entrant
- Other signs of significant deterioration
If any of these conditions exist, then evaluate the hose assemblies for correction or replacement. It is important you address these issues properly, as it can save you a lot of resources.
Functional Tests
Functional tests determine if the systems are leak free and operating properly. Always carry out functional tests per information from equipment manufacturers.
Test the system at maximum operating pressure and check for leaks or malfunctions. Ensure that the hose assembly is not operating beyond the maximum working pressure. The fluctuations in pressure should also be within the specified range for the hose assembly.
This can help assure that the hose assembly will not fail in the system and clarify any needs of correction or replacement.
Carrying out a functional tests at times leads to shutting down of the operation completely or partially. The benefit of visual inspection is that it can be done even when the systems are in operation.
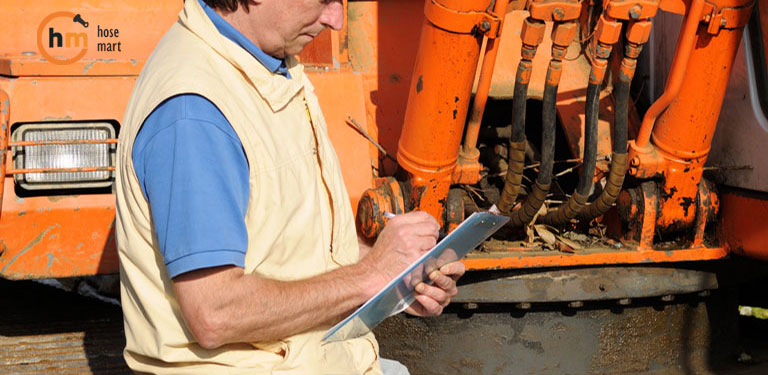
Steps to Create a Hose Maintenance Program
Now that you know the importance of a continuous hose maintenance program, we will help you draw the steps of making a hose maintenance program.
1. Identify all your Hose Assemblies
In this step, you identify all the hose assemblies operating in your work station or factory. It is important you tag them and store the details for future reference.
The details that you should record,
- Length of Hose
- Assembly Specifications
- Hose ID (inner diameter) and Construction
- Operating Conditions
- Cleaning Procedures
- Date of Installation
- Scheduled Replacement
The list does not end here but these are a few things which you definitely take a note of.
2. Regular Inspection & Tests
We recommend following a continuous hose maintenance schedule. Inspection and tests are of two types,
- Visual
- Functional
We have discussed this is detail above and therefore we will not be repeating it here.
This is the most crucial step of the program, the set of future actions will depend on the results of inspection and tests. The two common decisions that are taken are if the hose or assembly require correction or replacement.
3. Look for Tensions on Hose Assembly and Eliminate Them
You should always check for that the hose assembly does not have any tension or strain over it. This impacts the service life of the hose drastically. Look for these following things,
- Hoses rubbing against equipment
- External heat sources
- Twisting and bending beyond specified limits
- Bending too close to the fitting
- Insufficient hose length
After identifying these, you should immediately plan for the corrective measures. This can reduce the service life of the hose significantly.
4. Protective Cover if Required
At times it is important you provide a protective cover the hose assembly and that would increase the service life of the assembly.
Thermo-sleeve, pvc hose guards, outer additional braids, metal springs etc are examples of hose protective covers. They prevent the hose from erosion and damage from external work environment.
5. Analysis
Analyse your data and look for patterns. These patterns will determine the life cycle of the hose and assembly. It will help you plan inventory and know the average time when a replacement or correction is generally required.
Any anomaly can then be easily spotted and a corrective course can be taken. Also if the data shows a particular hose is being replaced too soon or too late. These insights can help you in big way to plan and control productivity.
6. Keep Spares Ready
From the previous step, you know the replacement intervals of the hoses and its assemblies. This can help you manage the stock properly. It is always a good a practice to have some additional stock of these following hoses and hose assemblies,
- Critical Process Application
- Safety Applications
- Applications where hoses are Very Likely to Fail
- Special Applications – replacements are not easily available
- Hose Assemblies which have a long lead time
This list also can be endless and there is no hard and fast rule. These are some of the applications in which we believe it is important you have spares ready.
This brings us to the end of the hose maintenance program.
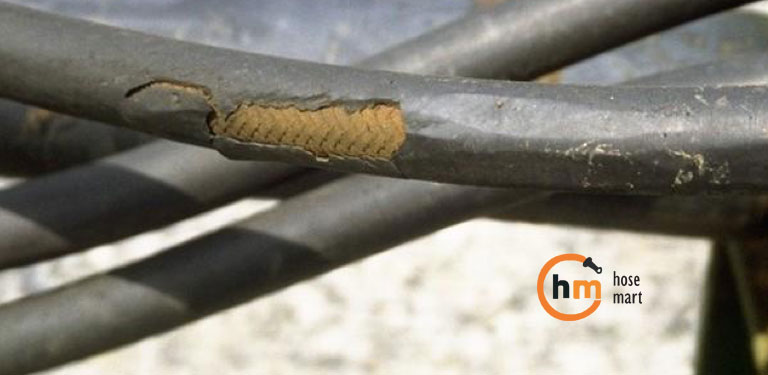
Conclusion
The hose maintenance program can help you make your work environment more productive and safer. We do always recommend doing a thorough safety check and hose maintenance.
You can always run the functional test before applying the hose assembly in the final system. After the assembly clears the functional tests, you should repeatedly carry out visual inspection and if need be, run periodic functional tests.
If you are looking for hose assembly, then we can provide you with it. Our facility is equipped to handle all your requirements and provide testing facility.
You can check out our online store or visit us. In case if you have any further questions you can always email us.